Introduction
The Indian manufacturing sector is changing, and fast. Manufacturers are adapting to smarter machines and connected systems. This shift is quietly putting India on the map as a competitive hub in the global supply chain.
Let’s delve into real world applications propelled by Industry 4.0 in India’s manufacturing sector. Discover recent trends and technologies which are shaping the future.
Inside the modern Indian factory
The workings of a modern Indian factory have changed. Industrial IoT (IIoT) networks track every step of production, from raw material intake to final dispatch. Smart manufacturing systems now rely on real-time data to adjust workflows and minimize waste. Machines are equipped with sensors and connectivity, which allow them to act as data points, enabling data analysis using AI algorithms.
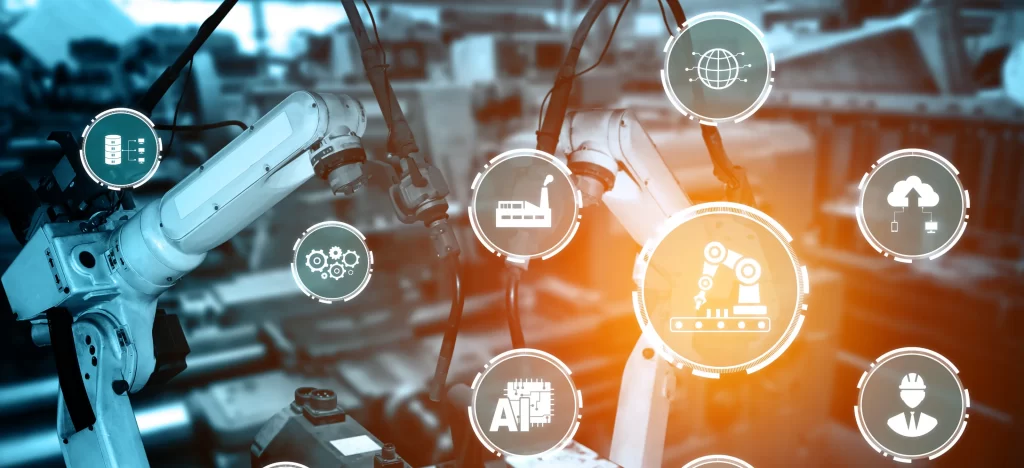
The technology behind the transformation
Industrial IoT (IIoT) connects machines, devices, and systems across the shop floor, allowing seamless communication and real-time data exchange. Artificial Intelligence (AI) is used to detect patterns, predict equipment failure, and guide quality inspections.
Smart dashboards ensure that data is processed efficiently. Meanwhile, AI algorithms allow manufacturers to simulate scenarios, test changes, and anticipate issues without disrupting operations.
India’s Industry 4.0 in Action
Across the country, leading manufacturers are already bringing Industry 4.0 principles to life. Tata Steel has adopted Industry 4.0, using IoT sensors and smart dashboards throughout its operations to improve equipment performance and operational transparency.
Cipla, the pharmaceutical company, has introduced smart manufacturing by integrating AI-powered analytics and Industrial IoT across its production lines. This enables early detection of quality issues and ensures compliance with pharmaceutical regulations.
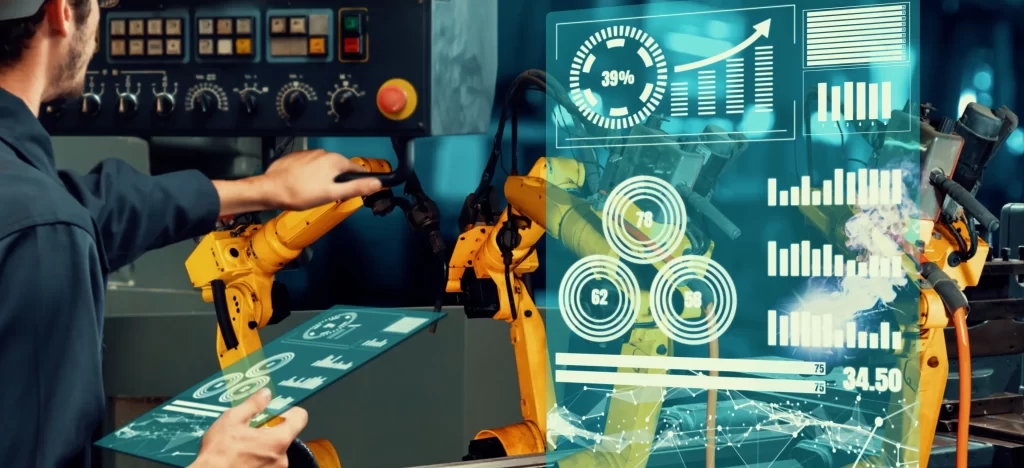
New trends powering the change
Manufacturers are moving toward smarter, more responsive operations. With real-time production data, factories are able to identify bottlenecks early, adjust workflows, and reduce downtime.
Many factories are also investing in AI-driven systems that support quality checks, predictive maintenance, and resource optimization. This helps boost both efficiency and consistency.
Smart dashboards give manufacturing teams a live view of key production metrics. This visibility helps managers make factual decisions and respond to issues before they escalate.
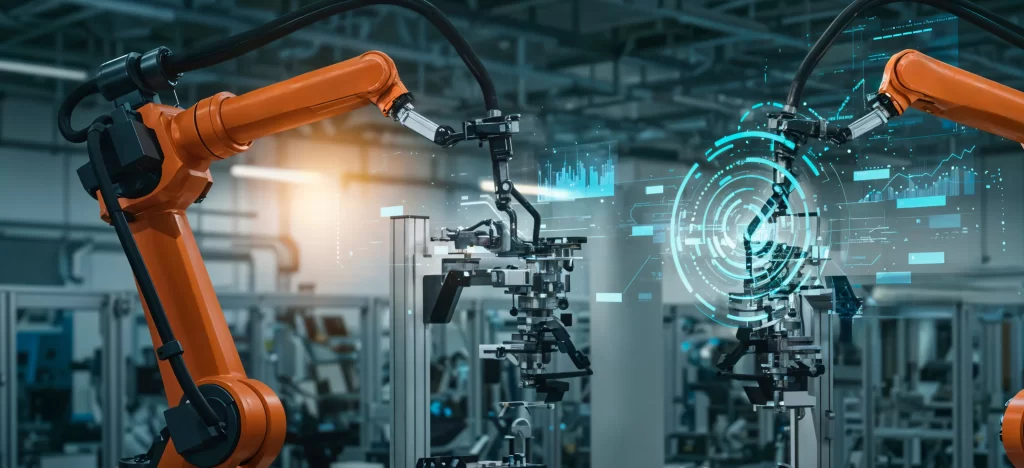
Conclusion
With the onset of Industry 4.0, India’s factories are becoming faster, smarter, and more agile. Industrial IoT and AI powered operations are helping manufacturers make quicker decisions, reduce downtime, and improve overall efficiency. The digital transformation has begun, and it’s only gaining pace.