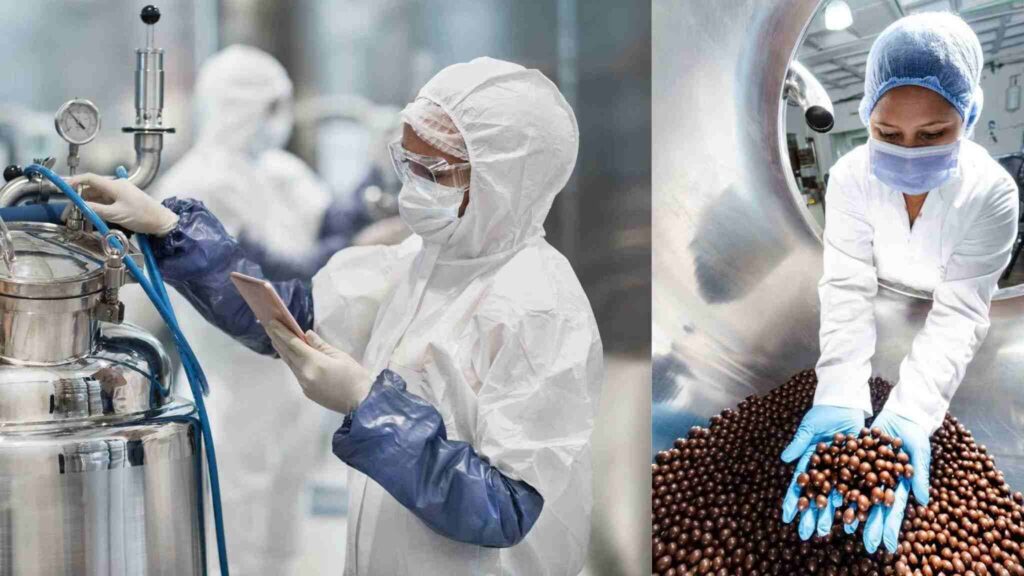
Success Story – Vistrian FactoryLOOK Implementation
North America’s largest cocoa processor and ingredient chocolate manufacturer selected Vistrian’s FactoryLOOK to monitor and manage operations effectiveness and key production processes in its manufacturing operations. This implementation has successfully been completed for one of the four manufacturing plants, with plans to roll out FactoryLOOK at the other plants in the next six months.
Initial Implementation: The customer started with an initial implementation at one plant to connect all production tools. The primary goal was to provide visibility and accountability using the Vistrian FactoryLOOK system in order to manage performance in process and equipment operations. Based on this customer’s unique requirements, the average number of parameters extracted from each of the production tools was 20 at a frequency of about 1 reading per second. While the customer had an existing supervisory control and data acquisition (SCADA) system, its reach was limited to engineering personnel at the plant. FactoryLOOK was selected to provide higher level access to all stakeholders within the enterprise by utilizing data from the SCADA as well as other software applications, and bring this data to one platform for universal access. FactoryLOOK provided dashboard views with accurate, real-time data tailored to each department within this organization.
Results from Initial Implementation: After FactoryLOOK was released into production, the FactoryLOOK software was able to provide efficient access to critical information and help detect previously unknown and unseen behavior from both the production tools as well as the process. Specific examples were:
- Some production tools (called refiners) were critical for the customer, since they constituted a bottleneck in the operation. It was essential to maintain a high level of utilization of these critical tools in order for this customer to maximize the plant throughput. The “Processing Rate” in the process of refining had variability driven by “batch ingredient ratio” as well as equipment set-up. Once FactoryLOOK was implemented, this customer was able to obtain continuous real-time visibility into the actual equipment utilization numbers. Since FactoryLOOK can be configured with complex rules to determine equipment productivity, accurate and realistic numbers for overall equipment effectiveness (OEE) were obtained by the customer, without human input.
In addition, the visibility provided by FactoryLOOK enabled the customer’s engineering department to definitively determine that the chief bottleneck to the plants output was actually the plumbing between the refiners and subsequent holding tanks, instead of deterioration in the refiners themselves, as was the previous assumption prior to FactoryLOOK implementation. This insight led the customer to avoid wasteful capital spending of over USD 1 million—which would have failed to address the real problem, as well—and instead spend a fraction of that amount on plumbing improvements. - The customer had problems obtaining accurate and timely reporting of production throughputs in the factory at each process step because of dependence on human data collection. Since implementation of FactoryLOOK, the operations managers are now able to obtain accurate production throughputs, including clear demarcation of shift and day boundaries.
- The customer had received complaints that the temperature of the liquid chocolate product was outside of the accepted range upon delivery to their destination site. The customer suspected this was due to the temperature of the product in the liquid holding tank prior to shipment. FactoryLOOK historian data that continuously records the temperature and provides real-time alerts of violations in temperature range was able to verify process compliance and eliminate expensive recall costs.
- A brand new robotic packing line had been recently installed at the factory. However, equipment performance was below expectations. Using FactoryLOOK’s online access to Event and Alarm Pareto charts, the equipment engineers were able to monitor and compare behavior of the robotic line over different days and shifts and come to a resolution of concrete steps they could take to improve productivity to expected levels. The ability to monitor robot events, and generate reports quickly was key to getting productivity improvements in a matter of days.
Based on the positive outcome and contribution of the first implementation, the customer plans to roll out FactoryLOOK across their remaining North American plants.
Subsequent Implementation: This customer’s management determined that real-time process and equipment data will help them improve OEE by over 20%, based on the preliminary results obtained above. Moreover, this first plant implementation demonstrated to the customer that investing in information technology solutions will provide added capacity without having to expand physical plant capacity, an idea they have now embraced.