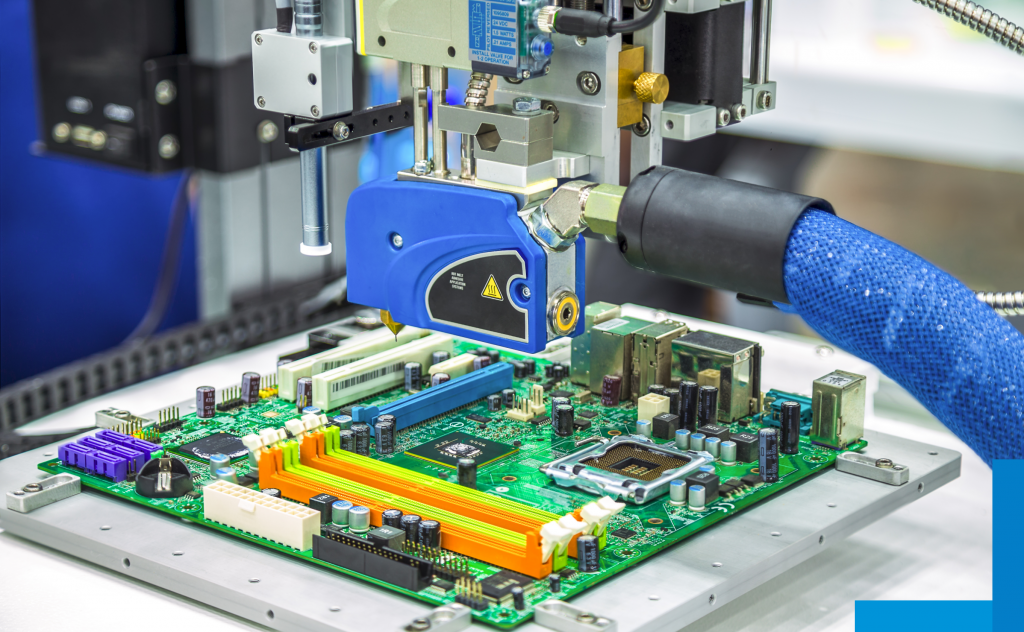
Success Story – Vistrian FactoryLOOK Implementation
A leading manufacturer of disk drives selected Vistrian’s FactoryLOOK to monitor and manage key production processes in their disk media manufacturing operations. What began as a small initial pilot program grew to FactoryLOOK implementation in 9 of their manufacturing plants, in 4 countries, across 300+ production tools, and in 90% of their production process steps.
Initial Pilot Implementation: The customer started with a pilot project consisting of 5 production tools spread across 3 production processes. The primary goal was to evaluate how useful FactoryLOOK would be in managing performance in process and equipment operations. Based on this customer’s unique requirements, the average number of parameters extracted from each of their production tools was 20 at a frequency of between 2-5 readings per second. In addition, the customer added a new type of sensor to one of the production tools to detect unusual disk behavior at one of their processing steps. Because the machine controller was inaccessible, we installed the Vistrian Spider to directly collect the sensor data on a continuous basis.
Results from Initial Implementation: After the pilot was released into production, the FactoryLOOK software was able to detect previously unknown and unseen behavior from the production tools as well as the operations staff. Specific examples of such behavior were:
- On some of the production tools, FactoryLOOK reported power readings on the ultrasonic generators that were surging to 4x the expected readings for a very short duration during each cycle. This was considered potentially damaging to the product, and FactoryLOOK’s report enabled the customer to take necessary steps to address this production tool and ultimately improve productivity.
- The throughputs of production tools were different and changing over time even though the process definition (recipe) used had not changed. FactoryLOOK was collecting cycle time information about the key bottleneck activity on the tool and was able to establish that the actual reason for the variance was that the pneumatic actuator that was slowly deteriorating, but had not yet failed. A casual observer of the tool’s operation would not have been able to capture this detail of tool behavior but FactoryLOOK’s data collection and analysis provided this customer a timely and preventative diagnosis of a production tool problem.
- Operators were resetting the error messages on the HMI system and continuing to operate a production tool even after a tool failure had been reported. While this behavior was suspected, FactoryLOOK provided clear records of this behavior by recording machine states on a continuous basis. This data provided the customer with sufficient cause to initiate operator re-training.
- The customer believed that equipment events/failures would lead to specific yield losses in production. However, there was no tangible data available about tool events in the past, since product failure analysis was only performed at the end of the production process. Using FactoryLOOK’s event and alarm trend charts, the customer was able to see a distinct correlation between equipment events and the corresponding yield losses. FactoryLOOK was able to provide this crucial intervention for the user to be able to foresee potential yield problems.
Based on the positive outcome and contribution of the pilot phase, this customer implemented the FactoryLOOK solution across a greater portion of their manufacturing process.
Subsequent Implementation: The customer implementedFactoryLOOK to cover 100% of tools in 2 critical operations and has chosen 2 other operations that are deemed important in their manufacturing process. The FactoryLOOK solution is currently implemented in 7 plants, in 4 countries and has grown to 300+ production tools being continuously monitored. In addition, 2 other product divisions and 4 additional plants in 3 countries have begun implementation rollout of FactoryLOOK.
Results from Subsequent Implementation: Upon successful implementation of the Vistrian FactoryLOOK system, the customer reported benefits in both production yield as well as equipment availability leading to a payback period of less than 6 months.