Introduction
Maintenance is the quiet engine behind manufacturing performance. When it’s reactive, it creates downtime. When it’s proactive, it drives reliability. VistrianMMS helps factories move from firefighting to foresight.
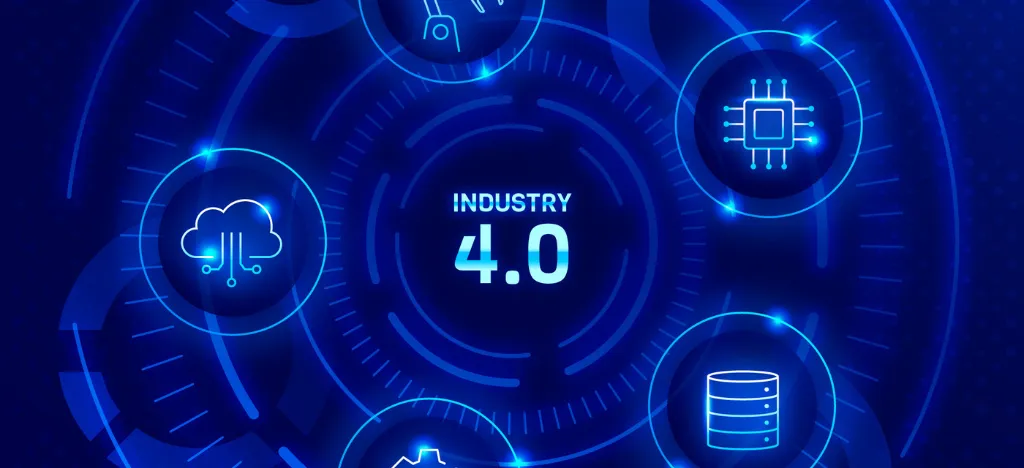
From Chaos to Control
The platform centralizes every maintenance task-planned, ongoing, or overdue-into one live, digital system. It connects work orders with equipment data, historical performance, and team workflows. No more spreadsheet chaos. No more manual logs. No more missed schedules.
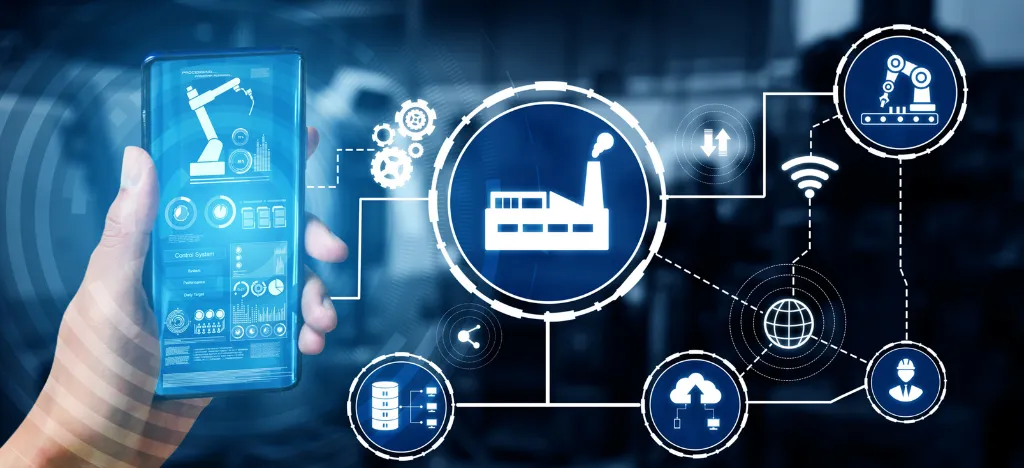
Smart Scheduling, Zero Surprises
With automated triggers based on usage, time, or real-time condition monitoring, VistrianMMS ensures the right task is performed at the right time. Maintenance teams can prioritize, assign, and track jobs from start to sign-off-boosting accountability and reducing downtime.
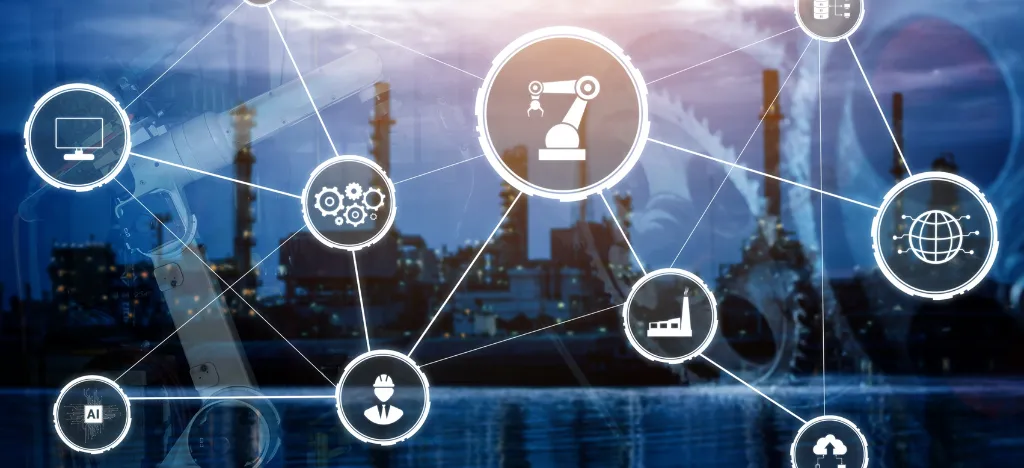
Clarity for Every Role
Maintenance managers get dashboards showing performance trends, recurring issues, and bottlenecks. Executives see cost impact and compliance in one place. Everyone moves with more visibility – and less uncertainty.
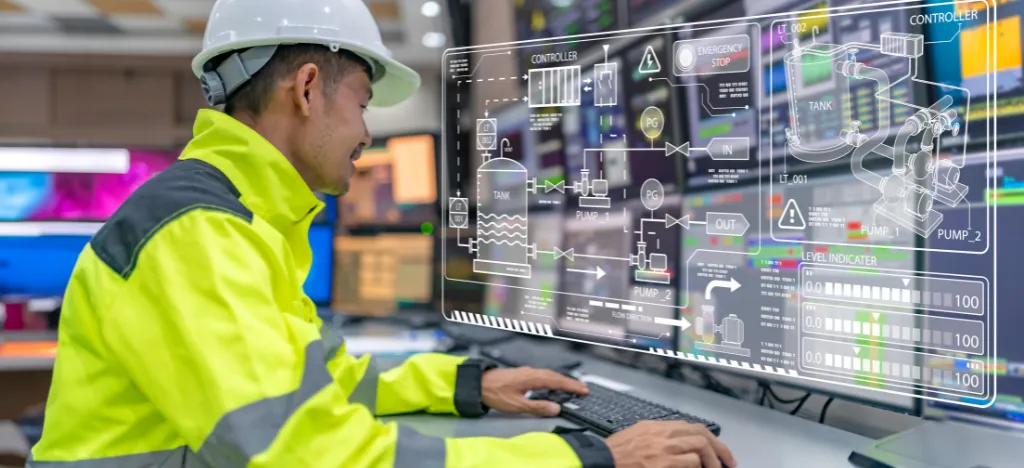
A Strategy, Not Just a System
Whether your factory runs 24/7 or in seasonal bursts, VistrianMMS adapts to your pace. It reduces unexpected breakdowns, extends asset life, and helps your team stay in control. In modern manufacturing, reliable maintenance isn’t just a function – it’s a strategy.